Overview
ENG_1003142.XML
G_PCS7_XX_00175
Integration and communication options with SIMATIC PCS 7 TeleControl
Plants are often scattered over very large grounds in the energy and transportation industries, and especially in the water & wastewater and oil & gas industries. In such cases it is necessary to integrate outstations for monitoring and controlling highly remote plant units, usually with a small or medium degree of automation, into the control system of the complete plant. This is carried out by means of telecontrol protocols over a WAN (Wide Area Network).
Conventional automation solutions for telecontrol systems use process control systems for the more complex central areas of the plant, and simpler Remote Terminal Units (RTUs) for the outstations, and then combine these separately configured plant units in a host network control system.
Direct integration of the telecontrol center
However, it is far more efficient if the telecontrol center for the RTUs is directly integrated into the process control system. The network control system as the superimposed integration level can then be omitted.
The SIMATIC PCS 7 TeleControl products are suitable for integration of the telecontrol center into the process control and engineering of the SIMATIC PCS 7 process control system. They support the RTU linking in various ways (see graphic "Integration and communication options with SIMATIC PCS 7 TeleControl" and table "Integratable remote stations – current range, communication options and features").
As far as the scope and performance of the automation functions are concerned, the requirements of the widely distributed plant sections are usually in the bottom to mid range, which means you can use automation stations of reduced dimensions for the outstations. SIMATIC PCS 7 TeleControl particularly supports the following outstations for distributed automation on site:
RTU type1)
|
RTU category
|
Possible telecontrol protocols
|
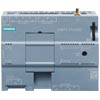 P_IK10_XX_01614 |
Compact telecontrol station SIMATIC RTU3030C with independent energy supply, e.g. from batteries, rechargeable batteries, solar panels
|
Very small with up to 16 I/Os
For very small applications
|
|
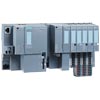 P_ST70_XX_07552 |
Controller integrated in SIMATIC ET 200SP
|
Small with 30 … 200 I/Os2)
For small applications
|
- Modbus RTU
- IEC 60870‑5‑101
- IEC 60870‑5‑104
|
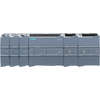 P_IK10_XX_01417 |
SIMATIC S7‑1200/S7‑1200F Controller
|
Small with 30 … 150 I/Os2)
For small applications
|
- DNP3
- Modbus RTU
- IEC 60870‑5‑104
|
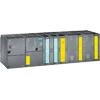 P_ST70_XX_04218 |
SIMATIC S7‑300/S7‑300F Controller
|
Medium with 100 … 2 000 I/Os2)
For medium sized applications
|
- SINAUT ST7
- DNP3
- Modbus RTU
- IEC 60870‑5‑101
- IEC 60870‑5‑104
|
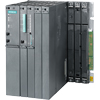 P_ST70_XX_04335 |
SIMATIC S7‑400/S7‑400F Controller
|
Large with 500 … 5 000 I/Os2)
For larger applications requiring higher performance
|
- SINAUT ST7
- DNP3
- Modbus RTU
- IEC 60870‑5‑101
- IEC 60870‑5‑104
|
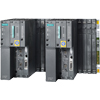 P_ST70_XX_06414 |
SIMATIC S7‑400H/S7‑400FH Controller
|
- DNP3
- IEC 60870‑5‑101
- IEC 60870‑5‑104
|
1) Also in version SIPLUS extreme, e.g. for environments with temperatures from -25 °C to +70 °C, condensation or exposure to environmental substances
2) Dependent on CPU size, protocol type, and application
For more information about telecontrol protocols, possible operating modes, and special remote configurations, see:
Note:
SIMATIC PCS 7 TeleControl V9.1 can be operated in combination with the OS Engineering software and OS Runtime software SIMATIC PCS 7 V9.1 as well as with PCS 7 PowerControl V9.1 (see section "Switchgear automation") and PCS 7 OPEN OS V9.1 (see section "Controller integration"). The SIMATIC PCS 7 software must be ordered from Catalog ST PCS 7.
Benefits
ENG_1003143.XML
- SIMATIC PCS 7 TeleControl cannot only integrate newly configured RTUs into SIMATIC PCS 7, but also migrate units which already exist in outdoor areas.
- As a result of its high level of integration, automation based on SIMATIC PCS 7 TeleControl offers decisive advantages compared to previous automation solutions with telecontrol engineering.
- The uniform SIMATIC PCS 7 software platform allows high efficiency during operation, and results in low costs for training, configuration and servicing.
- The homogeneous GUI for local and remote processes simplifies operation and simultaneously reduces the risk of an operator error.
- The Data Base Automation (DBA) software efficiently supports engineering and takes into account the conformity with SIMATIC PCS 7.
- DBA considerably facilitates project-specific adaptation of the system and importing of existing configurations in the course of migration.
- Extensions can be added during plant operation.
Application
ENG_1003144.XML
Remote control and monitoring of distributed stations, as well as data recording and transmission, with the following focal points:
- Water industry
- Well, pumping and slide valve stations in water supply networks and irrigation plants
- Pumping and slide valve stations in water and wastewater pipelines
- Storm-water tanks and siphon stations in wastewater networks
- Storage units (elevated tanks)
- Oil and gas industries
- Compressor, pressure reduction, transfer, block valve, and metering stations in gas networks
- Pumping and slide valve stations in oil pipelines
- Automation on the wellhead of gas and oil wells
- Stations for the injection of water or CO2 in gas or oil fields
- Energy management, environmental protection, and transportation
- Equipment for power generation and distribution
- District heating
- Traffic control systems
- Tunnels
- Railway stations
- Lighthouses
- Environmental monitoring equipment
- Weather stations
Design
ENG_1003145.XML
The telecontrol center for the outstations (RTU) is integrated into the process control of the SIMATIC PCS 7 process control system in the form of an Operator Station in single station or server design (also redundant as option). No additional automation system for conditioning and connecting telecontrol-specific data need be planned in the SIMATIC PCS 7 system. With large quantity frameworks, a PCS 7 TeleControl Operator Station (single station/server) is preferably responsible only for the telecontrol mode (dedicated). With small quantity frameworks, a server or a single station can also control SIMATIC PCS 7 automation systems in central plant areas in addition to the RTUs (dual-channel mode).
To enable engineering of the PCS 7 TeleControl Operator Station (single station/server), the functions of the Engineering Station of the SIMATIC PCS 7 process control system are expanded by DBA technology (Data Base Automation) and the SIMATIC PCS 7 TeleControl block library.
For communication with the RTUs, SIMATIC PCS 7 TeleControl uses the telecontrol protocols SINAUT ST7, DNP3 and Modbus RTU (via serial as well as TCP/IP communication connections) and also IEC 60870‑5‑101 (serial) and IEC 60870‑5‑104 (Ethernet TCP/IP).
With serial RTU interfacing, the telecontrol connection can be implemented cost-effectively at the control center end (PCS 7 TeleControl OS as single station or server) using the following components:
- SINAUT TIM communications modules
(SINAUT ST7 telecontrol protocol)
- TCP/IP serial converter
e.g. devices from the companies MOXA or Lantronix (telecontrol protocols DNP3, Modbus RTU, IEC 60870-5-101)
Remote stations can be connected either directly via Ethernet TCP/IP or via TCP/IP WAN routers to the SIMATIC PCS 7 plant bus (telecontrol protocols SINAUT ST7, DNP3, Modbus RTU, IEC 60870‑5‑104). When using the SINAUT ST7 telecontrol protocol, the SINAUT TIM communications module can be used in addition to the TCP/IP WAN router or as an alternative.
The table "Integrable outstations" shows the current connection possibilities depending on the type of RTU and type of communication.
Outstations for integration (RTU) Current range, communication options and features
|
Telecontrol protocol
|
SINAUT ST7
|
Modbus
|
DNP3
|
IEC 60870-5-101
|
IEC 60870-5-104
|
Type of communication
|
Serial
|
Ethernet TCP/IP
|
Serial
|
Ethernet TCP/IP
|
Serial
|
Ethernet TCP/IP
|
Serial
|
Ethernet TCP/IP
|
Interface on the PCS 7 TeleControl OS
|
TIM 4R‑IE
|
TCP/IP WAN router or/and TIM 4R‑IE
|
TCP/IP serial converter
|
TCP/IP WAN router
|
TCP/IP serial converter
|
TCP/IP WAN router
|
TCP/IP serial converter
|
TCP/IP WAN router
|
RTU/ interface
|
RTU3010C
|
–
|
Integrated
|
–
|
–
|
–
|
Integrated
|
–
|
Integrated
|
RTU3030C
|
–
|
UMTS integrated modem
|
–
|
–
|
–
|
UMTS integrated modem
|
–
|
UMTS integrated modem
|
RTU3031C
|
–
|
UMTS integrated modem
|
–
|
–
|
–
|
UMTS integrated modem
|
–
|
UMTS integrated modem
|
RTU3041C
|
–
|
LTE-M, NB-IoT modem integrated
|
–
|
–
|
–
|
LTE-M, NB-IoT modem integrated
|
–
|
LTE-M, NB-IoT modem integrated
|
ET 200SP with CPU 1510SP-1
|
–
|
CP 1542SP-1 IRC
|
–
|
CPU + software
|
–
|
CP 1542SP-1 IRC
|
CM PtP + SIPLUS RIC library
|
CP 1542SP-1 IRC or SIPLUS RIC library
|
S7‑1200/ S7‑1200F
|
CP 1243‑8 IRC
|
CP 1243‑8 IRC
|
CM 1241 + SW library
|
CPU + SW library
|
–
|
CP 1243‑1 DNP3
|
–
|
CP 1243‑1 IEC
|
S7-300/ S7‑300F
|
TIM 3V‑IE
|
TIM 3V‑IE
|
CP 341 + SW library
|
CP 343 + SW library
|
TIM 3V‑IE DNP3
|
TIM 3V‑IE DNP3
|
CP 341 + SIPLUS RIC library
|
CP 343 + SIPLUS RIC library or integrated PN interface + SIPLUS RIC library
|
S7‑400/ S7‑400F
|
TIM 4R‑IE
|
TIM 4R‑IE
|
CP 441 + SW library
|
CP 443 + SW library
|
TIM 4R‑IE DNP3
|
TIM 4R‑IE DNP3
|
CP 441 + SIPLUS RIC library
|
CP 443 + SIPLUS RIC library or integrated PN interface + SIPLUS RIC library
|
S7‑400H/ S7‑400FH
|
TIM 4R‑IE
|
TIM 4R‑IE
|
ET 200M + 2 × CP 341 + SW library
|
CP 443 + SW library
|
TIM 4R‑IE DNP3
|
TIM 4R‑IE DNP3
|
ET 200M + 2 × CP 341 + SIPLUS RIC library
|
CP 443 + SIPLUS RIC library or integrated PN interface + SIPLUS RIC library
|
Third-party station
|
–
|
–
|
Depends on type of station
|
Depends on type of station
|
Depends on type of station
|
Dial-up lines
|
●
|
–
|
–
|
–
|
–
|
–
|
–
|
–
|
Dedicated lines and wireless networks
|
●
|
●
|
●
|
●
|
●
|
●
|
●
|
●
|
Master/slave
|
●
|
●
|
●
|
●
|
●
|
●
|
●
|
●
|
Peer-to-peer
|
●
|
●
|
–
|
–
|
–
|
–
|
●
|
●
|
Mesh networks
|
●
|
●
|
–
|
–
|
●
|
●
|
●
|
●
|
Time stamping in RTU
|
●
|
●
|
–
|
–
|
●
|
●
|
●
|
●
|
RTU time synchronization
|
●
|
●
|
–
|
–
|
●
|
●
|
●
|
●
|
Data buffering in RTU
|
●
|
●
|
–
|
–
|
●
|
●
|
●
|
●
|
S7 routing
|
●
|
●
|
–
|
–
|
–
|
●
|
–
|
●
|
International standard
|
–
|
–
|
● (many variants)
|
● (many variants)
|
●
|
●
|
●
|
●
|
The telecontrol protocols used by SIMATIC PCS 7 TeleControl for remote communication are matched to the conditions of the widely distributed communication infrastructure.
The WAN transmission media suitable for communication between the RTUs and the telecontrol center are diverse, e.g.
- Private networks
- Wireless
- Dedicated line
- WLAN
- Public networks
- GPRS
- EGPRS
- UMTS
- DSL
- LTE-M
- NB-IoT
Based on the four basic topological forms (point-to-point, multipoint, star and ring), differently structured telecontrol networks can be implemented with these media variants, e.g. star over wireless, dedicated line or DSL. Through a combination of several basic topologies of the same or different media variants, it is also possible to design more complex network topologies, even with redundant communication paths. Optimum adaptation to the local conditions and the infrastructure which may already exist is possible in this manner.
Migration of existing telecontrol systems
SINAUT ST1 stations based on SIMATIC S5
For migration of existing plants, RTUs based on SIMATIC S5 can also be integrated via SIMATIC PCS 7 TeleControl into the process control system. In the process, the ST1 telecontrol protocol is converted into the ST7 protocol in the central TIM communications module.
Units with Modbus RTU communication
Existing units that have a Modbus infrastructure, even those outdoors, can be integrated into SIMATIC PCS 7 using SIMATIC PCS 7 TeleControl. These sections can be integrated into SIMATIC PCS 7 using the Modbus RTU protocol via serial lines or TCP/IP connections.
Whereas RTUs with Modbus TCP/IP interface can be integrated directly, third-party RTUs require special interface converters for telecontrol communication.
Third-party stations with telecontrol protocols
In addition to the Modbus RTU telecontrol protocol, the DNP3 (serial and TCP/IP), IEC 60870-5-101 (serial) and IEC 60870-5-104 (TCP/IP) telecontrol protocols also support the control center connection of third-party RTUs for migration. A prerequisite is that the RTU supports the corresponding protocol and that the required interface converters are available.
Third-party stations with OPC
Third-party RTUs for which an OPC server exists can be integrated into the process control with the PCS 7 TeleControl Operator System using additional engineering services on the basis of the DBA technology. SIMATIC PCS 7 TeleControl then supports data exchange between the Operator System (OPC client) and the RTU (OPC server) per OPC DA. The integration of RTUs via OPC UA is enabled with PCS 7/Open OS.
SINAUT LSX systems
Existing SINAUT LSX systems can also be migrated with SIMATIC PCS 7 TeleControl. The SIMATIC S7 controllers with the EDC telecontrol protocol (Event Driven Communication) installed in the SINAUT LSX system are integrated into SIMATIC PCS 7 TeleControl with PCS 7 TeleControl S7 EDC drivers (for ordering data, refer to the following catalog section PCS 7 TeleControl Operator System). Because the SINAUT LSX system can coexist at all levels next to the new system architecture as long as necessary, step-by-step modernization is possible without short-lived intermediate solutions.
Mode of operation
ENG_1003146.XML
With SIMATIC PCS 7 TeleControl, the outstations can be integrated into SIMATIC PCS 7 so that the operator notices no difference between central or remote automation with regard to the operating philosophy and alarm response.
The OS clients of the client/server multi-user system are able to display data from RTUs and SIMATIC PCS 7 automation systems (AS) - which they receive from a server with dual-channel functionality or from two separate servers - together in one process image. Display is primarily on faceplates for process objects such as motors, valves etc., but also by means of trend curves and messages.
If the PCS 7 TeleControl OS server is of redundant design, the redundant pair of PCS 7 TeleControl OS servers matches all internally generated information, e.g. alarm states and results of calculations.
The communication mode between the control center and RTU depends on the type of WAN, the configuration of the telecontrol communication, and the support by the telecontrol protocol.
Function
ENG_1003147.XML
Conditioning and display of data on the PCS 7 TeleControl OS (single stations/servers) are carried out by SIMATIC PCS 7 TeleControl blocks present in a library. These blocks support operator prompting in conformance with SIMATIC PCS 7 using symbols and faceplates, and also the hierarchy of the SIMATIC PCS 7 alarms.
Special blocks in combination with SINAUT ST7 and IEC 60870‑5‑104 enable integral use of the Industry Library in S7‑300 as well as S7‑400 RTUs.
In addition to blocks for processing of process data, the library also contains blocks for diagnostics and control of communication. If necessary, the supplied basic library can be extended using the DBA Type Editor by new script-based block types specific to the project.
Engineering can be automated efficiently and in conformance with SIMATIC PCS 7 using the DBA technology. DBA supports plant expansion during ongoing operation, and facilitates project-specific adaptation of the system as well as importing of existing configurations.
When linking RTUs by means of the SINAUT ST7, DNP3, IEC 60870‑5‑101 or IEC 60870‑5‑104 telecontrol protocol, the raw data in the remote stations is provided with a time tag and transmitted to the PCS 7 TeleControl OS (server/single station) acting as control center. Adaptation, further processing and archiving are carried out there. This procedure is appropriate for the event-based principle of operation of the telecontrol protocol as well as the subsequent chronological processing of data which was buffered in the remote station.
The time and date of the remote stations connected per SINAUT ST7, DNP3, IEC 60870‑5‑101 or IEC 60870‑5‑104 can be synchronized by the PCS 7 TeleControl OS (time master). Switchover between daylight-saving time and standard time is also taken into account.
In order to comply with guidelines, statutory directives and standards it may be necessary to provide special proof, e.g. proof of conformity with the ATV M260 guideline for sewage treatment plants. For this we recommend the ACRON software package equipped with even more functionality for long-term archiving and logging. ACRON is an add-on product in the Catalog ST PCS 7 AO (Add-ons for SIMATIC PCS 7).
More information